Why Commerce Wants Robots to Fix Themselves
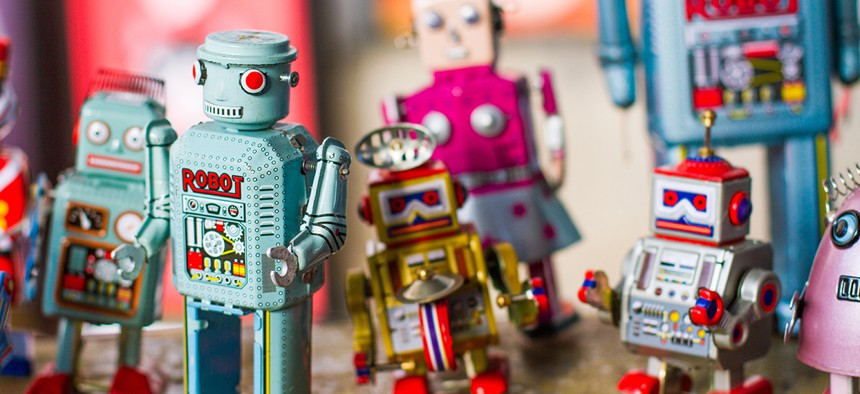
Caracarafoto/Shutterstock.com
NIST wants to create a standard test by which manufacturers can evaluate robots’ agility before deploying them in the factory.
American manufacturers would use more robots in their factories if there were a standard way to evaluate how agile those robots are, according to a federal research group.
The National Institute of Standards and Technology is collecting information about a workplace simulation that could test how well robotic systems deal with everyday manufacturing challenges, such as pivoting to new jobs or repairing parts, the agency announced last month.
Nextgov spoke with NIST group leader Craig Schlenoff about how agile robots can contribute to U.S. productivity. This conversation has been edited for length and clarity.
NG: How are today’s manufacturing robots falling short?
CS: Robots aren’t agile. Robots are very good at doing the same activity over and over again. Robots in car manufacturing, they’re huge robots and thousands and millions of times they’re moving parts from one location to another and they do it very accurately.
But there’s a lot of assumptions in the environment: that things are going to be in the same place when the robots pick it up and where it needs to put it down is always in the exact same location. When you have a more dynamic environment in which you have parts coming and they’re not in perfect configuration, and you have different products that you need to create, that paradigm doesn’t work as well.
We’re trying to get the robot to be more responsive to the environment. If a robot is moving a part from one location to another, and that part drops out of its gripper, if that were to happen in a plant, that part of the plant would have to shut down and probably some red lights would be flashing.
We’re trying to get the robot to be more knowledgeable about itself and the environment so that if it does drop a part, number one, it can recognize that it actually dropped the part . . . [and say,] “OK, the part is now here. Can I reach it or not reach it ?” ... And essentially have the robot have some level of intelligence so that it can complete the task even when failures happen.
NG: Why is it so difficult to build agile robots? When, realistically, could agile robots meaningfully improve manufacturing?
CS: One challenge is from the perception side. To get a robot to understand what objects are within the environment is actually very difficult. But once you perceive things in the environment, understanding ... what the parts are, what they can do, understanding that screws can screw into certain holes and tools have certain uses is knowledge that we have in our minds, but it’s very hard to put that knowledge inside a robot.
Having the robot understand where things are and what the most effective way of getting from one state to another, essentially from one product to another, is a challenge. On TV, we see things like "Star Wars," we see robots doing very very sophisticated things. The state of the art of robotics isn’t anywhere close to being there yet.
Test cases have been done by now, but they’re mostly research type cases. To get it to the point where it’s being useful by industry, maybe five years. Maybe five to 10 years.
NG: Are there any practical benefits to the federal government?
CS: We’re building test methods in order to assess how well robots can perform certain actions. We’ve done it for urban search and rescue ... based on test methods, we’re able to put together a good spreadsheet [ranking robots]: “With respect to mobility, here’s how well the robot did. With respect to perception, here’s how well the robot did.”
Based on that information, people in the Department of Homeland Security used it to say, “OK, we need to procure a whole bunch of robots. Let’s look at this big spreadsheet.”
But we’re now moving to do the same kind of thing in the manufacturing world.
NG: In designing the manufacturing simulation, NIST has asked industry to share what automation challenges they’re facing in the workplace. What have they told you?
CS: Have you been to IKEA? You go to IKEA, and there’s usually a bunch of screws. That bunch of screws is considered a kit. They also have kits for people on the plant floor that are doing assembly. Maybe a person in some location is responsible for putting something together and they have a kit of parts.
The process of creating that kit is one of the things they’re looking to automate. Instead of it being a very manual task, somebody goes out and gets 10 screws and four washers, they want to use robots to put together these kits and then give it to the people down the assembly line. Moving forward, we want to certainly do more sophisticated assembly.
(Image via Caracarafoto/Shutterstock.com)