3D Printing and Legos: Perfect Together
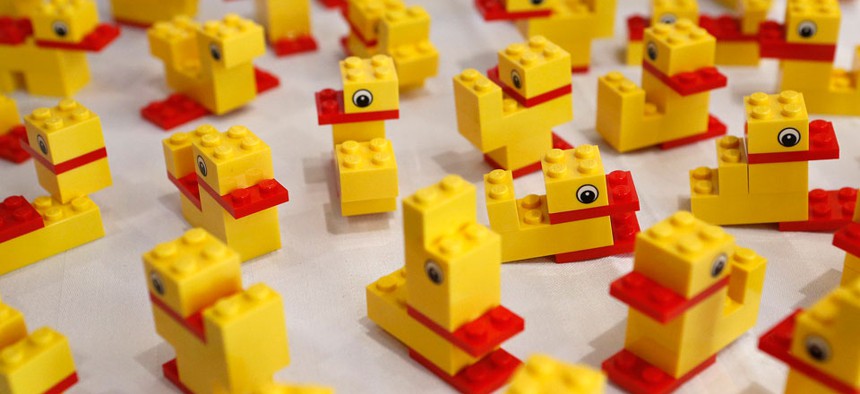
Ducks created with LEGO bricks LEGO Foundation/AP
New software allows designers to "legofy" their prototypes, eliminating hours of time spent waiting for 3D printers to churn out their widgets.
But it's a slow thrill.
3D printing, even for a small object, can take a loooooong time. If you're just trying to make a little widget on a one-off basis, (say a piece for a board game or something), a little wait while one strip of plastic is extruded upon another is no big deal. But for professional designers, speed is, doctoral student Stefanie Mueller says , "mission critical."
According to Mueller, designers often allow their plans to print overnight, so as to waste less time. But that limits them to "a single iteration per day." Over a whole design process, that really gums up the works. "A typical iteration process when refining a prototype easily adds up to a week—even though the actual design work may not have taken longer than a day," she wrote to me. The whole process gets bottlenecked at the 3D printer.
This is why Mueller built faBrickator , a program that marries 3D printing with a building material beloved around the world: Legos. Using faBrickator, designers can sub Legos into their designs, and only print small pieces.
For example, Mueller says, consider this design for a head-mounted visual display glasses:


For such a project, the details of the casing will require less attention than the part around the lenses, which will need to be tinkered with until the right optical path is achieved. To print the entire thing takes about 14 hours, Mueller says. But the whole thing doesn't need to be printed each time to perfect just one part. With faBrickator, Mueller explained to me, designers can "mark the lens mounts as 'high-resolution'," which will leave those parts for the 3D printer. "faBrickator then exports these parts for 3D printing and generates instructions that show users how to create everything else from Lego bricks. If users iterate on the design later, faBrickator offers even greater benefit as it allows re-printing only the elements that changed."
She demonstrates how that works in the video below:
Mueller says that many experienced designers do this kind of blending of 3D printed bespoke parts and existing materials already, but doing so "requires a good amount of ingenuity and experience." With faBrickator, built at the Human Computer Interaction Lab at Hasso Plattner Institute , designers easily play with which parts need to be custom built and which Legos can easily substitute. After all the parts are perfected, designers can revert the whole project to 3D printing, and drop all the Legos out.