Creating the next-generation manufacturing world
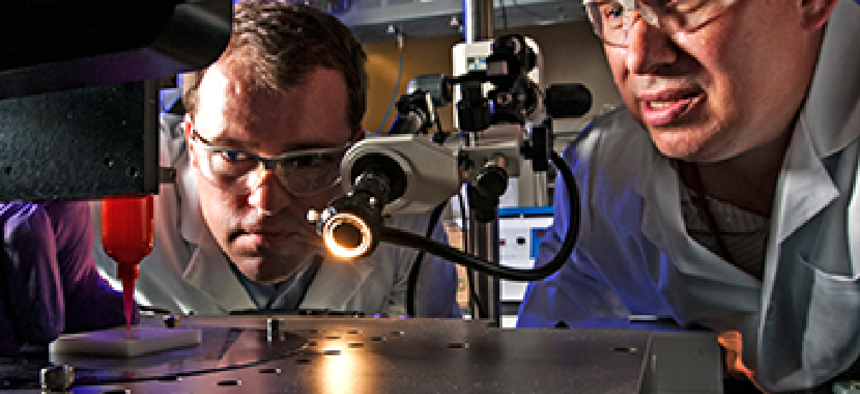
Lawrence Livermore National Laboratory is teaming with Autodesk to research advanced applications for 3D printing.
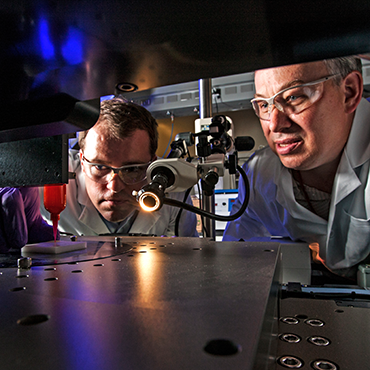
LLNL engineers Eric Duoss (left) and Tom Wilson use an additive manufacturing process called direct ink writing to develop an engineered "foam" cushion. (George Kitrinos / LLNL)
Under a cooperative research agreement with the company that helps create digital worlds in Hollywood blockbusters, researchers at Lawrence Livermore National Laboratory are experimenting with design software that could help create radical versions of everyday things.
LLNL and Autodesk Inc. signed an18-month cooperative research and development agreement, under which LLNL will use Autodesk software for generative design to study how new material microstructures, arranged in complex configurations and printed with additive manufacturing techniques (essentially, 3D printing), can be used to produce objects with physical properties that weren’t feasible before.
Through its various operations, Autodesk has provided autoCAD programs to industry, as well as digital effects programs to movie producers. Its software was behind many of the special effects in in James Cameron’s 2009 film “Avatar,” as well as other films.
Under the deal, researchers will use additive manufacturing, material modeling and architected design -- which involves arranging materials at the micro and nanoscale through computational design -- to fuel new manufacturing processes using high-performance computing and generative software.
The collaboration will initially create protective helmets as a test case, to study how to improve design performance. Advanced additive manufacturing techniques will allow more complex microstructures that could result in lighter-weight helmets capable of absorbing and dissipating more energy more predictably than traditionally manufactured helmets. LLNL hasn’t determined exactly what kinds of helmets will be made, but sports helmets, including football, baseball, biking and skiing, are possible, Eric Duoss, an LLNL materials engineer and the co-principal investigator for the agreement, said in an Aug. 17 joint statement with Autodesk.
But researchers say the helmets are just a first step.
By applying goal-oriented design software tools, LLNL and Autodesk expect to generate and analyze the performance of very large sets – thousands to tens of thousands – of different structural configurations.
Researchers envision a future where any product can be composed of bespoke materials that are optimally built on both a micro and macro scale, incorporating new materials arranged in new ways.
“Giving the software goals and constraints as input, then allowing the computer to synthesize form and optimize across multiple materials, will lead to the discovery of unexpected, high-performing designs that would not have otherwise been pursued,” said Mark Davis, Autodesk’s senior director of design research.
NEXT STORY: Can Metrics Capture the Value of 'Innovation'?